- Point of view
Process mining in the supply chain: Making sense of a complex world
How process mining can improve business performance, agility, and profitability
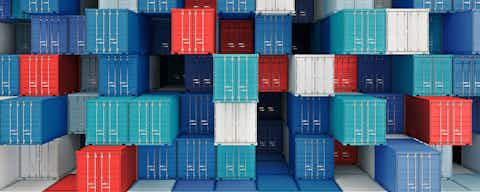
Ask any supply chain leader to outline their organization's delivery process and they will likely produce a standard journey that starts with order placement and ends with order closure.
But take a closer look at the average customer's actual journey and things may be far less straightforward, as increased complexity within the supply chain prompts businesses to make manual interventions, process deviations, and exceptions to complete each order.
The result? The average delivery process is often anything but standard.
Process mining – optimizing business processes through event log data analysis – is a way for organizations to visualize how processes within the supply chain actually run, as opposed to how they ought to. Using advanced data and analytics capabilities, organizations can draw insights from operating systems to improve visibility and transparency within the supply chain, identify root causes of inefficiencies, and trace how they manifest throughout the business.
Though process mining holds extraordinary potential in terms of improved customer service, reduced excess inventory, and decreased manufacturing and logistics costs, the total value cannot be unlocked by a single use case. Rather, process mining is an iterative, progressive process; initial use cases provide the foundation for more advanced capabilities, building value and compounding returns over time.
At a glance: the value of processes mining within the supply chain
- Increase customer service level by 2-10%
- Release 5-10% of capital tied in inventory
- Reduce manufacturing and logistics costs by 5-10%
Here, we explore several common process mining use cases within the supply chain and the steps organizations can take to optimize their standard processes—from start to finish and everywhere in between.
A closer look at process mininguse cases in the supply chain
Process mining use cases fall into two distinct categories:
- Execution performance
- Planning performance
Execution performance
Execution performance use cases use process mining to provide visibility and transparency into the thousands of daily transactions within the business' various operating systems, such as the warehouse management system, transportation management system, manufacturing execution system, or enterprise resource planning (ERP) system. In so doing, the organization can proactively identify potential performance issues, as well as pinpoint the root causes of inefficiencies and underperformance. In the most advanced scenarios, transactions may be automatically adjusted to optimize performance.
Planning performance
Planning performance use cases focus on mid-term supply chain planning. In these use cases, the organization will leverage data from the business' operating systems to correct planning parameters based on demonstrated process performance. In so doing, plans are easier to execute, which in turn results in higher business performance.
In advanced cases of planning performance, process mining can enable decision mining and elevate planning processes, such as sales and operations planning and integrated business planning . You can read more details on decision mining use cases here.
Common process mining use cases in the supply chain
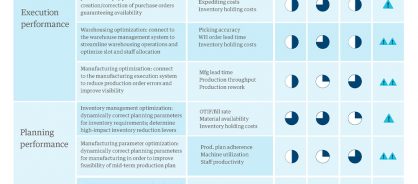
Identifying a high-value, foundational process mining use case
Selecting an initial use case to jump-start the organization's process mining journey is an extremely important decision because it will test the business' technology capabilities and influence the deployment of future use cases. We recommend selecting a use case based on two distinct criteria:
- Anticipated value delivered to the business
- Ease of implementation.
Though the value of the use case will depend on each business' unique goals, customer service is widely regarded as a top priority. As such, use cases that focus on increasing service levels are strong candidates for process mining.
To gauge the ease of implementation, supply chain leaders must first evaluate the digital maturity of the system or systems they intend to mine. For example, if the source system has few data errors and event logs are rigorously created at a granular level, then implementation of the process mining use case will take less effort. Moreover, if the source system is widely used – as ERP systems are, for example – it's likely that the process mining technology vendor has developed data connectors it can reuse with little effort.
In most client engagements, we recommend beginning the process mining journey with the on-time-in-full (OTIF) management use case because it generally delivers high value to the business and is relatively easy to implement. In addition, the OTIF management use case is based on order-to-cash processes, a popular application of process mining, so it's likely the process mining technology vendor has already developed applications or services.
With an OTIF use case in place, the next logical use case to implement in the supply chain is wider inventory management optimization.
How to improve OTIF management using process mining
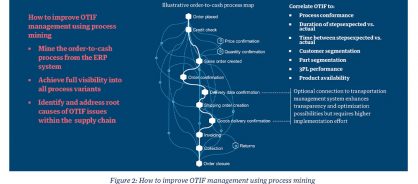
Case Study
How a consumer electronics manufacturer jump-started its process mining journey with OTIF management
Over the past few years, the European branch of a global consumer electronics manufacturer has experienced strong sales growth. But the organization's delivery capabilities couldn't scale to meet this new demand. Customers experienced long delays and miscommunication, leading to poor satisfaction rates.
Though sales remained high, the organization recognized that its current growth trajectory couldn't continue unless the business optimized the order management process.
It set out to tackle the problem with supply chain and operations leaders and found a flaw in the dataset that made it impossible to identify the root cause of delays or even accurately measure performance.
The manufacturer engaged us to help improve visibility and transparency within the order management process using process mining. We identified three key objectives:
- Achieve process transparency by understanding the reality of the order management process in its full complexity
- Increase customer service levels by identifying and fixing the root causes of late or incomplete deliveries and eliminating unnecessary process complexity
- Sustain the achieved benefits as sales continue to grow and complexity naturally increases
Improving OTIF through process mining
The team extracted data from the ERP system to develop a comprehensive process map. Within six weeks, it had generated an initial set of insights to determine the cause of the lackluster OTIF rate. This allowed the team to design improvement initiatives that addressed those specific pain points within the order process.
What process mining uncovered:
- One in three orders deviated from the standard process, resulting in more than 100,000 process variants
- About 60% of orders had significant high-effort manual process changes that increased lead time from 14 days to 39 days on average
- Erroneous credit holds and delivery blocks caused delays that reduced OTIF by an average of 12%
- Misclassification of products as long-term reserved reduced the OTIF rate by 16%
Results: optimizing the supply chain through OTIF improvements
A 14% improvement in the OTIF rate was achieved by:
- Increasing the first-time-right rate from 40% to 80%
- Instituting rule-based automated correction of credit hold and delivery block errors
- Optimizing product reservation logic
- The average lead time decreased by 10 days – from 29 days to 19 days – by minimizing or eliminating rework and automating lengthy manual activities
- The ratio of order lines managed per employee rose from 11,000 to 30,000 via automation, error correction, process streamlining, and the implementation of new policies
Enable a new competitive advantage through process mining
Extreme levels of customization enabled by digital technology and rising customer expectations are increasing business complexity. Organizations that do not address these core issues and how they manifest throughout the business face eroding margins and lost revenue. On the other hand, businesses that adopt process mining technology are developing a new kind of competitive advantage – the ability to thrive in complexity.