- Case study
Digitally transforming order management for a semiconductor parts manufacturer
How a global supplier of semiconductor spare parts and services improved parts fulfillment and cut downtime for clients.
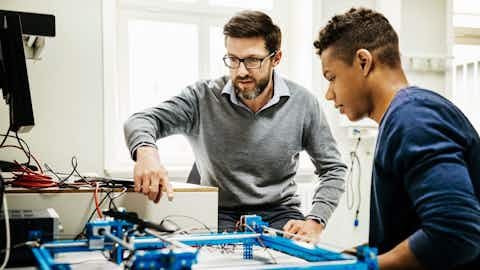
Who we worked with
A global supplier of semiconductor fabrication equipment and services
What the company needed
To improve its spare parts and servicing operations performance, with a focus on order management and escalation processes to drive efficiencies, boost productivity, enhance collaboration, and improve customer experience.
How we helped
After a thorough assessment of the current state of spares and service operations, we identified and prioritized opportunities for improvements across reverse engineering and order management.
What the company got
- Measurable benefits from high-level implementation across planning and optimization, intelligent order fulfillment, touchless order processing, supplier collaboration and integration, and case management
- Identification of productivity savings of 50–70% globally
- Recommendations to boost customer satisfaction through a reduction of errors and downstream disputes
Challenge
To minimize downtime in the fabrication process
Capacity utilization is critical for foundries, and downtime costs millions of dollars for every minute wafer fabrication equipment fails. It is critical, therefore, for suppliers of wafer fabrication equipment to have streamlined processes and systems for parts fulfillment and replacement to minimize downtime for their clients.
For this manufacturer, the major challenges in doing so lay across order management and reverse engineering. Employees were struggling with legacy systems, leading to 60–70% manual intervention. And the need to work with fragmented tools across multiple teams and fulfillment scenarios added complexity.
The team identified major issues across:
- Planning and optimization: The company lacked planning processes for repairs, demand visibility for aging parts, inventory visibility and optimization, and supply constraints
- Order fulfillment and processing: The team did not have real-time inventory visibility, leading to conflicting customer service priorities, complex communications, and high dependency on suppliers for parts availability
- Supplier collaboration: The company's suppliers, planning, and case management processes were not integrated
- Case management: Poor data quality was causing delays, and the team was grappling with a lack of clear data rules, a high need for human interaction, missed windows of opportunity for free-of-charge services, and reactive processing
All these challenges led to a lack of productivity and poor employee experience, as well as reduced customer satisfaction due to delayed deliveries and a high need for communications and returns.
Take a copy for yourself
Solution
Reimagining spare order management processes
Genpact completed a deep-dive assessment of the company's spare parts order management and operations. This included performing a gap analysis and identifying potential opportunities for improvements across people, processes, and digital tools.
We then reimagined the spares order management process with a multipronged approach. This included:
- Optimization of demand and planning processes for repair operations through increased supply chain visibility, including the predicting of part failures with machine learning (ML) models. This enables maximized output with reduced inventory
- Intelligent order fulfillment using a digital workbench platform that orchestrates data and analytics across systems to enable order management teams to make informed, real-time decisions
- Touchless order processing using ML-enhanced Esker and SAP software capabilities to process all standard orders with low or no human touch
- Supplier collaboration and integration, bringing together planning optimization and case management processes with repair suppliers to establish an exceptions-based process with a reduced need for human intervention
- Intelligent case management using digital twins and internet of things solutions to automate the distribution process and ensure that the right parts ship to the right place at the right time. This eliminates unnecessary logistics costs and reduces aging parts in circulation
Impact
Reduced cycle time and downtime, and increased productivity
The company now has a defined implementation roadmap that provides clear next steps and the business benefits of taking them. The impact of the transformation of spare parts and service operations includes:
- Reduced overall cycle time with increased free-of-charge output from suppliers
- Reduced employee effort on collaborative tasks by 60–80%
- Accurate allocation of inventory based on demand and orchestration of processes, leading to a 50–70% boost in productivity
- Automated orders leading to a 40–60% spike in productivity
- Complete integration with suppliers on case management and planning processes to streamline communications and reduce cycle time by 30%
- Significantly improved on-time delivery of parts through the reduction of out-of-stock situations
Overall, the roadmap identifies key areas for elevating employee experience while reducing costs and enhancing efficiency, and ensures customer satisfaction by keeping the machines that power the increasingly vital semiconductor industry running.