- Case study
One small step for an aerospace firm is a giant leap forward for intelligent automation
A plan to put AI in place takes flight
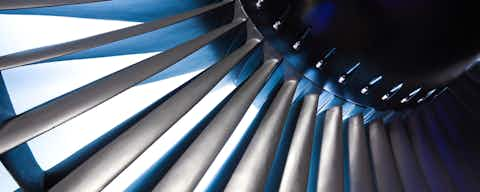
Who we worked with
One of the world’s largest and most innovative aerospace manufacturers and service providers.
What the company needed
The client was looking to take advantage robotic process automation (RPA) technology to reduce costs, improve quality, increase productivity and reduce exposure to risk in its shared services center. With limited RPA experience, they turned to Genpact to help.
How we helped
Genpact suggested that RPA could enhance intelligent automation capabilities, potentially paving the way for future artificial intelligence (AI) integration. So we first assessed the company's processes and digital tools to determine its readiness for RPA. Then we designed and activated a center of excellence (CoE) and an RPA pilot program that would put the company on the runway.
What the company got
Productivity savings of 30%–50%, thanks to RPA. The pilot alone delivered $3 million in savings, covering the costs of development. We helped the client to scale, starting with three automated processes in Q2 2017 to over 100 processes and 100 bots by Q2 2018. The company expects to see an 8x ROI over three years, and realize $200 million in savings with intelligent automation over the next five years.
Challenge
Bring on the bots – the right way
Our client, one of the world’s largest aerospace manufacturers, wanted to use RPA to help drive down costs, improve quality, enhance overall productivity, and enrich the user experience. The firm has a blend of managed services and shared services, but limited experience with digital technologies, so it realized it couldn't go it alone. It needed a helping hand if it wanted to automate at scale within its scheduled time frames.
Genpact began by first identifying the processes best suited to deliver value and support the CoE we were designing. The processes we chose with the company ranged from validating in-flight shipping information from freight forwarders to finance and accounting processes.
Solution
Develop an intelligent automation flight plan
The firm wanted to secure its position as an innovation leader and asked Genpact to support its RPA launch given our existing relationship with them. We had already improved its shared services operations, saving it $250 million since 2015.
For this new effort, we introduced the concept of using RPA as a starting point. The plan was to start using the Genpact Cora – our digital business platform that brings together AI and advanced technologies in a modular and governed way – to introduce dynamic workflows. And embed artificial intelligence across multiple business groups and functions. A CoE was also planned to successfully lead and scale the initiative.First, we assessed the company's IT readiness for RPA, identifying anything that could pose short- or long-term challenges. Then, to demonstrate how everything would work, we designed a model for what would become the digital labor CoE.
As part of the design, we selected and prioritized processes for automation that would have minimal risk and business disruption. We helped identify software vendors that would support the company's digital labor transformation, and we provided recommendations for governance and implementation.
After the client signed off on the design, we spent 12 weeks adding staff to the digital labor CoE, getting its IT environment ready to scale and putting the pilots into production.
Impact
Soaring productivity and sky high savings
With its digital labor CoE and the flight plan Genpact developed, the company:
- Made automation possible across all business functions with a digital workforce of 100 bots live within a year, automating around 200,000 hours
- Boosted revenue by improving competitive advantage through innovation and faster operations
- Achieved eightfold ROI during the project duration
- Improved compliance and lowered risk of manual errors
- Achieved $200 million in savings over five years