- Case study
Refreshing product quality and employee safety at SodaStream
How automation transformed global processes and future-proofed operations
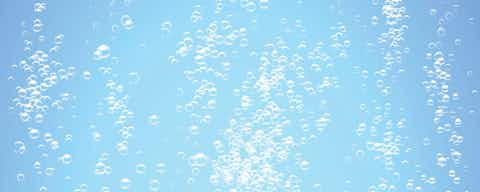
Who we worked with
SodaStream is a global manufacturing company best known for helping people transform ordinary tap water into sparkling water at the touch of a button.
How we helped
- Ran workshops with SodaStream to understand user requirements
- Used Genpact's Cora Orchestration and Microsoft's Azure solutions to design the system
- Built, implemented, and continually refined the system, dubbed SodaFlow
What the company needed
- To create a centralized product quality and employee safety management system
- The ability to spot and act on discrepancies and non-conformities within the system
- To future-proof operations by digitizing existing and largely manual processes
What the company got
- A connected, multilingual system to manage product quality and employee safety
- Secure, digital workflows delivering process insights at a local and global level
- An opportunity to manage other business processes using the same scalable system
Challenge
A global business with local processes
Across its vast supply chain, SodaStream deals with hundreds of partners and vendors, and having so many moving parts can make transparency tricky. But SodaStream never compromises on quality. It uses a range of controls at each step of the supply chain to meet its high production and employee-safety standards.
Unfortunately, manufacturing-line processes were largely manual. If an employee spotted a hazardous situation – at a site in the US, Israel, the Netherlands, Australia, Canada, Germany, or China – there were many ways to resolve it. This lack of consistency made it difficult to act on any red flags quickly.
To future-proof its operations, SodaStream needed a partner to connect, digitize, and automate processes at a global level. An end-to-end centralized view of what's happening across the supply chain is essential to maintaining its quality and safety standards.
Solution
A better way of working built on automation
SodaStream partnered with Genpact to develop a cloud-based system to manage product quality and employee safety. For the Genpact team, the first stage was to explore this goal in more detail. What steps should the process include? Which employees should have access? Which languages should it support? Genpact ran several workshops with SodaStream stakeholders to discuss the requirements for the new system.
Based on the workshops' findings, the next step was to design a system with Microsoft's Azure and Genpact's Cora Orchestration technologies. Azure is a cloud-computing service that helps organizations build, manage, and deploy applications at scale. Built on Azure, Cora Orchestration uses agile methodologies to visualize workflows before, during, and after implementation. This allowed employees to test the system before it went live and make recommendations that Genpact could address instantly.
With so many data sources running through the system, SodaStream also needed to ensure that moving to the cloud would not put the business at risk. Both Microsoft and Genpact follow the highest standards of security and compliance, so SodaStream was confident that the system was secure.
After thorough planning, design, and test phases, the system – SodaFlow – was ready to get to work.
Impact
Connected people, processes, and technology
SodaFlow, built on the latest cloud and automation technology, is flexible and scalable. In less than six months, SodaStream was using the system across six global sites in multiple languages. It's accessible on both mobile and desktop devices, and SodaStream can spot hazardous trends more easily so that employees can prevent a red flag before it becomes a major issue.
Integration with existing compliance systems was also hugely important to future-proofing the product quality and employee safety. This integration allows SodaStream employees to address discrepancies, non-conformities, and complaints directly within the system.
SodaFlow gives managers the insights and analytical tools they need to create realistic benchmarks and KPIs – something that wasn't feasible with the previous system. It also provides a single source of truth for quality and control information across a global supply chain.