- Case study
Smooth operator: Fueling supply chains with better data
How an energy and petrochemical company gained end-to-end supply chain visibility
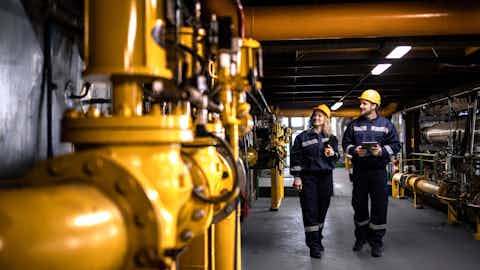
Who we worked with
A subsidiary of one of the largest publicly traded international energy and petrochemical companies.
What the company needed
Complete global supply chain visibility and a single source of truth for its supply chain planners to better forecast supply and demand and free up working capital.
How we helped
We built and delivered a global control tower using o9's cloud-based software to empower supply chain planners to collaborate and effectively use supply and demand data. We supported the design of new planning processes to drive operational efficiencies across regions, redefining planner roles in the process.
What the company got
The company achieved a savings of over $35 million in working capital (inventory reductions) by:
- Reducing raw material safety stocks
- Decreasing the lead time by two days in a high-traffic lane in Asia
- Harmonizing regional processes
- Saving time on daily tasks and analysis
Challenge
No single source of truth for supply chain planners
When the company came to Genpact and o9, it had a clear but complex problem – a lack of visibility across one of its supply chain divisions was causing inefficient inventory management and tying up working capital.
In some regions, it was storing too much raw material; in others, too little. And the visibility problem sometimes led to stock overproduction. Plus, the company's fragmented technology landscape added to the confused view of the value chain – each geography used its on-premises version of SAP and Blue Yonder. Misaligned systems and gaps in data governance made it harder to trust planning tools, so planners resorted to offline collaboration and manual workarounds to get necessary answers. It became evident the company had to invest in data, technology, and processes to support its customers better.
Solution
A supply chain control tower for near real-time monitoring of demand and supply signals
We helped the company with its digital and process transformation. The solution was straightforward – an improved and global control tower to provide a single source of truth for this business unit's supply chain planners.
Genpact and o9 worked closely with the company to deliver the new control tower over five key stages.
- First, we worked with regional supply chain leads to understand the challenges specific to their region
- Then, we worked with the client to create a strong data foundation for the supply chain control tower. Plus, we defined role-based governance processes
- While work on the control tower kicked off, we designed, built, and published reports that gave planners visibility into orders, forecasts, and inventory status so they could target some quick wins like avoiding stockouts
- Together with the company, we designed and deployed a system that generates alerts in response to material and capacity shortages. We prioritized these alerts based on risk margins, enabling planners to act quickly. We also introduced scenario modeling to estimate the effects of significant supply chain changes, ranging from bill of materials (BOM) adjustments to adding or removing a shipping lane between plants
- In the final phase, we connected the company's carriers through a third-party aggregator to enable real-time intranetwork and outbound shipment tracking. We integrated warehousing and manufacturing data to achieve near real-time visibility into production status parameters such as batch expiry, tank levels, line run rates, and production line performance
We managed the project's blueprinting, use case generation, functional design, user acceptance testing, and training. o9 managed technical design and functionality build for this global supply chain visibility solution.
Impact
A transparent and resilient supply chain
The global control tower gives the company complete visibility over one of its value chains. It also delivers more advanced insights, such as the potential impact of strikes or port congestion, enabling its supply chain team to manage inventory better and get ahead of problems.
The control tower helps the company adapt to market shifts with a more robust and flexible supply chain and exceed customer expectations. Our control tower solution has contributed to reducing supply chain operating costs and improving working capital on both raw materials and finished goods by over $35 million. It also helps planners avoid stockouts and write-offs by creating alerts for impending events and initiating a problem-resolution workflow. The company can now hold reduced raw material safety stocks. Planners can observe the downstream impact on customer orders and prioritize top customers when needed. Overall, the company has maximized its savings and optimized its ability to deliver customer orders on time in full.
The company was so pleased with the impact of our work on its supply chain that the team asked us to help streamline its manufacturing and warehousing units too. There's no better review than being trusted to solve new problems.
Supply chain management
Boost sustainable growth and resilience with our supply chain management solutions.
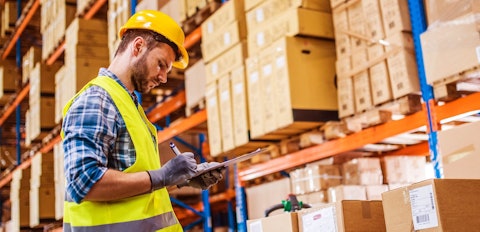