- Case study
Optimizing the supply chain of a major American food corporation, step by step
How Genpact's logistics center of excellence continuously improves the food and beverage giant's supply chain
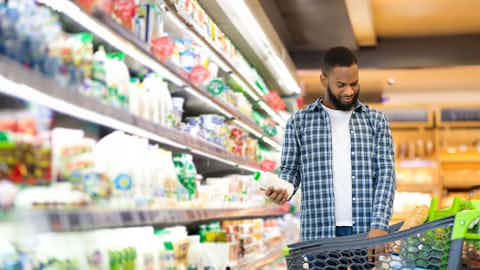
Who we worked with
One of the largest global food and beverage companies with a supply chain that stretches across more than 100 manufacturing partners, 40 factories, and 88 distribution centers.
What the company needed
- To identify opportunities to redesign the supply chain and reduce inefficiencies by increasing analytical, data-driven decision-making
- Network enhancements that support the business' growth plan
How we helped
- Established a logistics center of excellence (CoE) to expedite supply chain efficiencies
- Optimized logistics and distribution networks
- Boosted profitability of its fleet and installed trackers to monitor monthly savings
- Automated processes to enable tactical decision-making and cost reduction
What the company got
- 1% cost savings opportunities, $10 million of which have been implemented over four years
- Better visibility of network flows and distribution bottlenecks
- Optimized customer sourcing
- Distribution models that evaluate overflows and nearby warehouse closures
- Supported analysis for manufacturing capacity constraints for many product categories
Challenge
Enhancing an already efficient supply chain network
It's a challenging environment for food and drink manufacturers. Branded items no longer hold the sway they once did as customers' tastes change or seek cheaper alternatives. Rising inflation and a looming recession compound these tough conditions.
Retailers, dealing with their own market headwinds, demand on-time, in-full (OTIF) deliveries from suppliers, often imposing fines for anything late or incorrect. Transport and logistics complications make agility a crucial characteristic of today's supply chains.
The company already had an efficient supply chain, but continuous network improvements and visibility of supply chain inefficiencies were crucial for delivering shareholder value and meeting annual savings targets.
With the company spending several billion dollars on manufacturing and distribution, there were opportunities to make the network more efficient. Additionally, low-volume stock was racking up supply chain losses.
But any updates to the supply chain would also need to help break down silos to better meet customer demand, support long-term investment strategies, and support the company's growth plan.
Solution
A logistics center of excellence to hunt out inefficiencies
The company needed a framework to continuously identify ways to improve supply chain performance. We knew more advanced analytical capabilities were vital to finding these opportunities, so we established a team of logistics and Coupa Supply Chain Modeler experts to design models that identify any gaps emerging between optimal operations and actual network performance.
This logistics CoE optimizes the supply chain for capital expenditure (CapEx) investments through long-range capacity planning, identifying manufacturing lines related to long-range capacity gaps and risks. To redesign the supply chain network, we established an optimal number and size of warehouses, closed overflows, and recommended regional distribution centers.
For non-CapEx investments, we used the production network's existing capabilities and capacities to make quick gains:
- Optimized the entire network's total cost to serve for some product categories, including transportation, and warehousing costs
- Improved customer sourcing and allocation changes, minimizing total costs and boosting service
- Adjusted delivery routes and service regions to increase the fleet program's profitability
- Reduced overall costs through automation that enables more tactical decision-making
- Implemented trackers to monitor monthly savings and analyze opportunities for further potential network changes
Genpact's logistics CoE and our client's team connect daily on operational inputs, required outputs, and recommendations.
Take a copy for yourself
Impact
Small wins, big gains
The insights from the logistics CoE into the company's supply chain network maximize network and product flows and minimize distribution bottlenecks. It builds and maintains optimization models that improve service and cost savings. Results include:
- Deeper knowledge of production splits, which allows our client's team to meet its forecasts
- Distribution models created by the CoE, which empower the company to understand whether to close overflows and nearby warehouses, expand regional distribution centers, or add new greenfield locations
- The ability to evaluate multiple what-if scenarios based on business requirements
Together, we've optimized the supply chain to reduce total cost to serve and service time for the end customer. This translates to 1% cost savings opportunities on total supply chain spend, with over $10 million in savings achieved over four years and $10 million in savings to be approved. We've also identified manufacturing line capacity gaps for 11% of overall product categories.
What's next?
The logistics CoE's focus is set to expand to optimize warehouse operations and the company's dedicated fleet. The team continues to refresh existing models, tools, and trackers every month to identify ongoing savings opportunities. We'll also add new automation tools and trackers to identify quicker ways to save.